The success of any geomembrane installation – safeguarding landfills, ponds, reservoirs, mines, or wastewater facilities – rests fundamentally on the integrity of its seams. Choosing the best HDPE liner welding machine is not just a purchase; it’s an investment in project reliability, environmental protection, and your professional reputation. A subpar machine or poor selection can lead to seam failures, costly repairs, environmental incidents, and significant delays. With various technologies and specifications on the market, navigating the options requires a strategic approach. This comprehensive guide details the critical factors to ensure you select the optimal HDPE liner welding machine for your specific operational needs.
1. Understanding Core HDPE Liner Welding Machine Technologies: Extrusion vs. Hot Wedge
Extrusion Welding Machines
Process: Utilizes an internal extruder to melt HDPE welding rod (filler material). This molten polymer is forced through a die onto the seam area, simultaneously melting the surfaces of the overlapping liner sheets. Pressure rollers then fuse the materials.
Key Advantages:
Hot Wedge (or Hot Air) Welding Machines
Key Advantages:
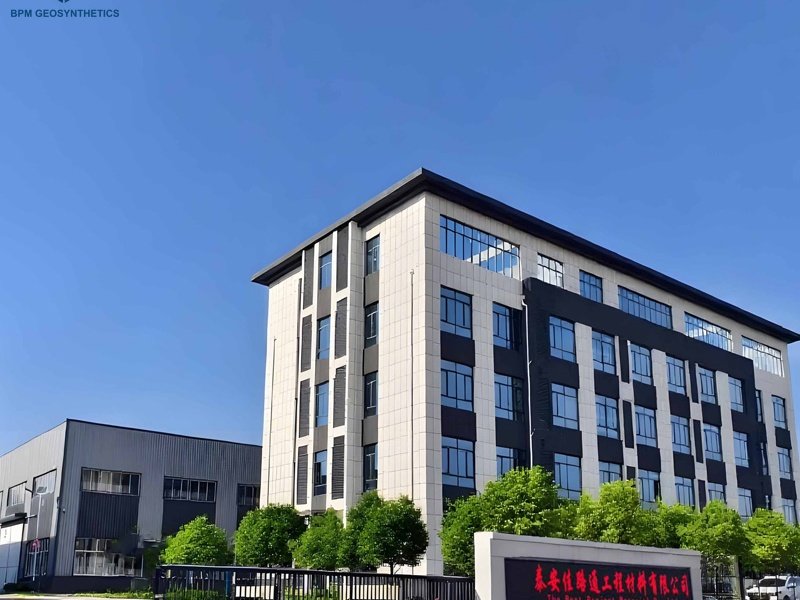
2. Defining Project Requirements: The Foundation for Your HDPE Liner Welding Machine Choice
Liner Thickness Range:
Seam Types and Complexity:
Production Volume & Project Scale:
Site Conditions:
Mandatory Seam Testing:
If contractual requirements dictate air channel pressure testing (common in landfills, potable water), a dual-track hot wedge HDPE liner welding machine is necessary to create the channel. Extrusion welds require vacuum box or destructive peel/shear testing.
3. Evaluating Critical HDPE Liner Welding Machine Specifications & Features
Power Source Compatibility:
Drive System Performance:
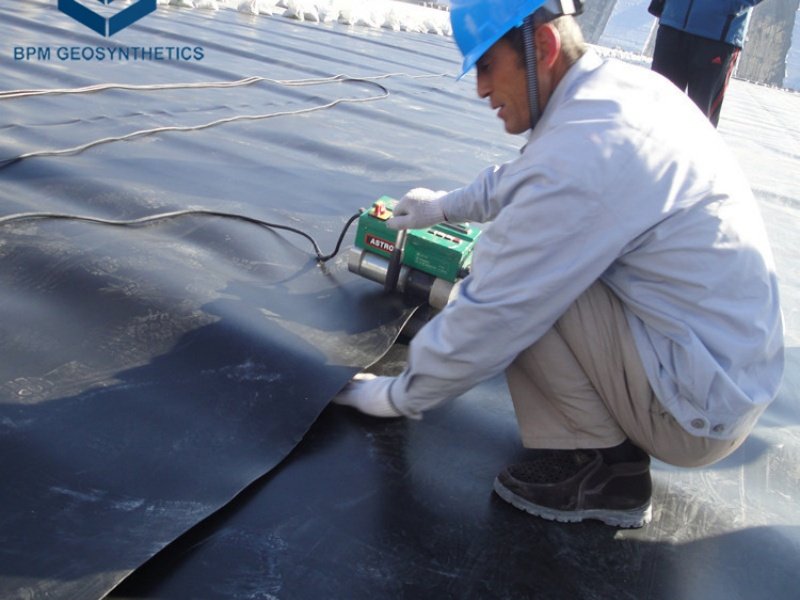
4. The Essential Support Ecosystem Around Your HDPE Liner Welding Machine
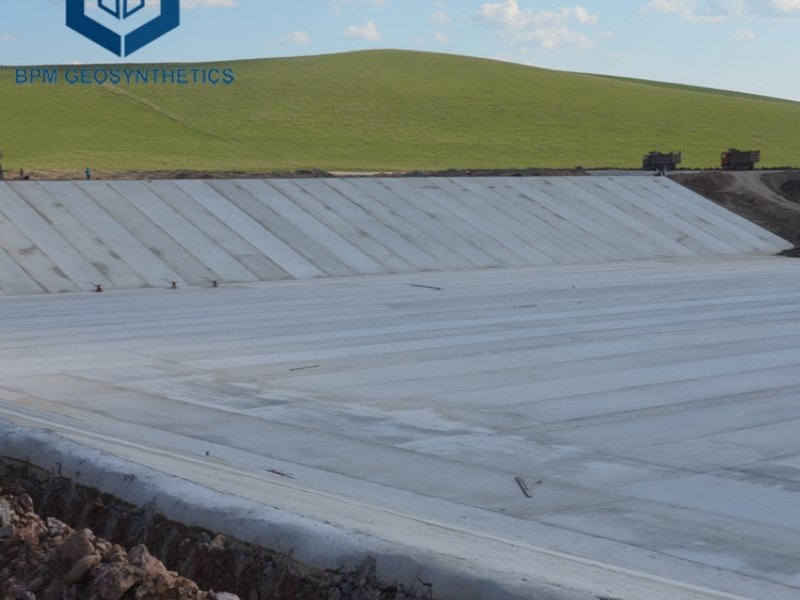